Sample for Safety Plan/HSE Plan you can also change as per your requirement (Company name must be change) if you want to download in word (doc) format link given below.
TABLE OF CONTENT
S. No | TITLE | PAGE |
1 | Introduction | 2 |
2 | Safety Policy | 3 |
3 | Management Participation | 4 |
4 | Leadership and Commitment | 4 – 5 |
5 | Supervisors Responsibilities | 5 |
6 | Employees Responsibilities | 5-6 |
7 | Safety Enforcement Plan | 6 |
8 | HSE Objective and Target | 6-7 |
9 | Sub-Contractor | 7 |
10 | New Employee | 8 |
11 | PPE | 8 |
12 | Training | 9 |
13 | Road Safety | 9 |
14 | Fire Protection | 10 |
15 | Heat Stress | 10 |
16 | Hoisting and Rigging | 11 |
17 | Housekeeping | 12 |
18 | Working at Height | 12-13 |
19 | Permit to Work | 13 |
20 | Electrical Safety | 13-14 |
21 | Sanitation on-site/plant | 14-15 |
22 | Hand and Power Tools | 15 |
23 | Scaffolding Safety | 15-16 |
24 | First Aid Plan and Facilities | 16-17 |
25 | Materials Handling and Proper Storage | 17 |
26 | Reporting of Incident/Accident/Near miss Procedures | 17-19 |
27 | Emergency Procedures | 20 |
28 | Daily Safety Check List Format | 21-23 |
- INTRODUCTION
This document defines the Safety Rules and Regulations to be implemented by COMPANY NAME in the execution of PROJECT NAME.
CLICK HERE FOR > EMERGENCY RESPONSE PLAN
CLICK HERE FOR > COVID-19 SAFETY PLAN
CLICK HERE FOR > HIRA
CLICK HERE FOR > JSA
CLICK HERE FOR > MONSOON SAFETY PLAN
CLICK HERE FOR > ENVIRONMENT MANAGEMENT PLAN FOR CONSTRUCTION SITE
This will serve as the guide to everyone in construction. It helps to regulate, prevent, and minimize the risks that caused possible losses of life of personnel, damage of property, equipment, time, money, and loss of reputation.
The company will provide safety precautions in every identified hazard and proper dissemination to everyone who will involve the exposure of critical activities. Each employee will be provided with the initial introduction and continuous training to enable him to perform his work safely.
Furthermore, these regulations comply with the safety requirements set out by the main contractor/client and the General Safety Policy of COMPANY NAME.
- SAFETY POLICY (Please attach your company HSE Policy)
OCCUPATIONAL HEALTH, SAFETY & ENVIRONMENT POLICY
“Safety of person overrides all the production targets” is the Health Safety and Environment policy of Company name.
Company name believes that all injuries, occupational illnesses as well as safety and environment incidents are preventable.
Company name is committed to:
- Conduct all its activities in such a manner as to avoid harm to employees, subcontractors and the community;
- Promote occupational health of its employees and sub-contractors.
- Sustainable development by continuously improving its environmental practices and performance;
- Implementing, safe operating procedures (SOPs) and controls and the relevant safety practices in construction activities;
- Company with all statutory requirements concerning Health, Safety and Environment;
- Create a culture of learning and practicing Health, Safety and Environment systems, procedures and practices among all its employees and sub-contractors;
- Endeavoring to develop the culture of resource conservation and pollution prevention;
- Providing awareness training to the concerned person who are directly associated with the construction activities at our project sites to ensure good HSE performance;
- Respecting the surrounding community and controlling environmental health hazards arising from operations and events as a result of the project site activities.
- Working as a team in our effort to achieve the objective of averting accident without harm and damage;
- Recognizing HSE management as shared responsibility at all appropriate levels
Date: 15/03/2018
Place: (Managing Director)
CLICK HERE FOR ? HIRA AND JSA
Safety is a team effort – Let us all work together to keep this a safe and healthy workplace.
3.MANAGEMENT PARTICIPATION
3.1 Ensure that a plant wide safety committee is formed and is carrying out its responsibilities as described in this program.
3.2 Ensure that sufficient employee time, supervisor support, and funds are budgeted for safety equipment, training and to carry out the safety program.
3.3 Evaluate supervisors each year to make sure they are carrying out their responsibilities as described in this program.
3.4 Ensure that all incidents are fully investigated and corrective action taken to prevent the hazardous conditions or behaviours from happening again.
3.5 Ensure that a record of injuries and illnesses is maintained and posted as described this program.
3.6 Set a good example by following established safety rules and attending required training.
3.7 Report unsafe practices or conditions to the supervisor of the area where the hazard was observed.
4.LEADERSHIP AND COMMITMENT
The Management of COMPANY NAME and various section heads are firmly committed to maintaining and continuously improving of HSE management system and to protect health, safety of Serious Services employees and also others who may be affected by its activities and to the protection of environment at all work places and will ensure that no environmental hazard will be created by the activities of Serious Services and sub-contractors.
S. NO | ACTION | ACTION PARTY | TARGET |
1 | Management visit to convey safety message, staff meeting and inspection/audit. | Project Head | Monthly |
2 | HSE Manager/ Quality manager visit for inspection, compliance audit, meeting, training and QHSE Workshop | HSE Manager/ Quality manager | Monthly |
3 | Continuation of award scheme and reward best employee of the month award to staff | Project Manager/ Site Manager | Monthly |
4 | Select best employee HSE award every year | Project Head/ Quality Manager/ Site Manager | Yearly |
5 | Meet the criteria of evaluation process for safety award | HSE Manager/ Quality Manager/ Site Manager | Yearly |
How to Make Safety Plan
- SUPERVISORS RESPONSIBILITIES
5.1 Ensure that each employee you supervise has received an initial orientation before beginning work.
5.2 Ensure that each employee you supervise is competent or receives training on safe operation of equipment or tasks before starting work on that equipment or project.
5.3 Ensure that each employee receives required personal protective equipment (PPE) before starting work on a project requiring PPE.
5.4 Do a daily walk-around safety-check of the work area. Promptly correct any hazards you find.
5.5 Observe the employees you supervise working. Promptly correct any unsafe behaviour. Provide training and take corrective action as necessary.
5.6 Set a good example for employees by following safety rules and attending required training.
5.7 Investigate all incidents in your area and report your findings to management.
5.8 Talk to management about changes to work practices or equipment that will improve employee safety.
- EMPLOYEES RESPONSIBILITIES
6.1 Observe the items of responsibility established in this document as well as job safety rules which may apply to specific task assignments.
6.2 Immediately inform the area supervisor the existing unsafe conditions in his area of responsibility and leave the work unless the corrective actions are in place.
6.3 Ensure the employees can fully comprehend the specific task assigned to him by his supervisor to avoid any untoward incident/accident in his area of responsibility.
6.4 Must wear appropriate PPE prior to start the work.
6.5 Cooperate during the inspection in his area of responsibility as well as the facilities surrounded in him.
6.6 Participate actively the trainings, seminars set by the company for the promotion of healthy and safe working conditions.
6.7 Must be keen always and maintain buddy system.
6.8 Follow and comply the risk assessment provided/instructed by the supervisor.
6.9 Working hours shall be observed always and maintain good attitude to his co-workers.
6.10 Do not attempt to execute the job if you’re doubtful the situation, immediately consult your supervisor.
6.11 Always think safety all the time before executing any task entrusted to you.
6.12 Be concern to your co-worker, be responsible and never let anyone get hurt by ignoring the safety.
6.13 Be friendly all the times; avoid fighting if possible to your co-worker because it will constitute immediate termination.
6.14 If you’re not feeling well seek medical assistance immediately and inform your supervisor.
6.15 Be tactful all the time and observed cleanliness in your area of responsibility.
6.16 Respect to your superior.
- SAFETY ENFORCEMENT PLAN
There should be a daily TBT (Tool Box Talk) on the job site for all workers by the crew leader and supervisor as per the activities and weekly HSE topics. The meetings will be conducted by Spig safety officer in conjunction with line supervisors and workforces. Indoctrination will include instructions on project safety practices, reporting of accidents, availability of medical facilities and individual responsibility in case of accidents during the course of operation. The agenda will be recorded in the logbook to be kept by the Safety Officer. COMPANY NAME Safety Officer must attend the scheduled meeting set by the General Contractor’s Safety Department either weekly or monthly. Safety Officer shall be copy furnished with every weekly/monthly meeting being conducted. Copy of each weekly/monthly minutes of the meeting will be posted at a conspicuous location at the jobsite.
- HSE OBJECTIVE AND TARGET
HSE OBJECTIVE
- Minimize Occupational health and risks through engineering Control, Administrative control, Hire and placement, Periodic inspection and maintenance of equipment.
- Minimizing Energy consumption.
- Minimizing fuel consumption.
- Procurement of equipment, automobiles, materials, etc with environmental considerations in focus.
- Improvement of indoor air quality.
HSE TARGET
LIST OF INDICATORS | HSE TARGETS |
1. Fatal | ZERO |
2. Road Traffic Incident Frequency (RTIF) | ZERO |
3. Loss Time Occupational ill Frequency | ZERO |
4. Loss Time Injury Frequency (LTIF) | ZERO |
5. Site Specific Risk Assessment (SSRA) | For each Activity |
6. Hazard Reporting | When Happen |
7. Work Place Inspection by Site In Charge | Everyday |
How to Make Safety Plan
- SUB-CONTRACTOR
The sub-contractors shall be subject to the same standard, as CLIENT NAME is required to comply in the performance of the contract. Regular audits/inspections will be planned and conducted to verify and assess the subcontractor’s compliance with HSE Management System.
The HSE Advisor will monitor sub-contractor’s compliance at site and non-compliance shall be reported to the site manager and contract manager for appropriate action.
Related HSE statistics of sub-contractors shall be included into COMPANY NAME statistics. All sub-contractors are accountable for their respective HSE performance and shall be required to meet Key Performance Indicator and targets in line with COMPANY NAME objectives.
The sub-contractors HSE Statistics shall be included in contract HSE Statistics. The sub-contractor’s performance shall be closely monitored and incorporated in the COMPANY overall HSE performance/Statistics.
The sub-contractor HSE Performance will also be included on the agenda of regular Serious Services HSE Management System reviews for this contract.
Control of Suppliers: Vendor/Supplier/Third Party Performing Services for COMPANY NAME or its sub-contractors that involve Journeys to site and irregular presence on site will not be required to prepare the HSE Plan. They will be monitored by Site Manager/Project Manager.
- NEW EMPLOYEE INDUCTION
All new employees of SPIG take mandatory HSE induction Training from CLIENT-HSE Department.
New coming employee upon his arrival on the project shall be instructed on HSE rules regulations
of company, Hazards and risk to explained.
- PERSONAL PROTECTIVE EQUIPMENT
Providing Personal Protective Equipment is one way of reducing, controlling the hazards associated in the jobs carried by the workers. Providing complete PPE’s means that each life is valuable compared to many factors involved in the project.
Personal protective equipment is available for your use. When equipment has been specified for certain work assignments or areas, you must use it.
- All employees, visitors and vendors must wear hard hats prior to enter the job site.
- Must wear clothing suitable for the work you are doing. Wear sturdy work shoes. Safety shoes are desirable.
- Must wear proper eye protection when you are exposed to flying objects, dust, chemicals.
- Hearing protective equipment is available upon request. May be required to use it in designated areas or for specific jobs.
- Respiratory equipment may be required in area where health hazards exist due to the accumulation of dust, fumes, mists or vapors.
- Safety harness and lifelines must be used when working above 1.8 meters.
- Wear gloves when handling objects or substances which could cut, tear, or burn the hands.
- Must wear rubber boots for work in concrete, mud or water.
- Hairnets may be required for employees whose hair is a potential source of injury.
- Head protection (Safety Helmet) and foot protection (Safety Shoes) shall be worn by all the employees while working at SITE. Safety belt with full-body harness shall be used while working at height > 1.8 M. Safety harness shall be anchored at the shoulder or above height.
Safety helmet shall be with ISI mark with chin strap. The Colour codes of the helmets shall be followed as mentioned below: –
How to Make Safety Plan
Supervisor/Engineers and above | White |
Safety Personnel | Green |
Workers | Yellow |
Electrician | Red |
Visitors | Orange |
- TRAINING
To achieve our HSE objective and to meet the ZERO Accident Targets, HSE training shall be regularly organized for all personnel working on Project. All managerial and supervisory staff shall attend HSE Training Courses, organized from time to time. Training register shall be attending training programs organized by the CLIENT as per the CLIENT training schedule
CLICK HERE FOR ? HSE TRAINING
13.VEHICLE AND ROAD SAFETY
The CONTRACTOR’s/ SUB-CONTRACTOR’s SM/SE/SO shall take care that all their vehicles entering the project SITE should have necessary documents & register the necessary details at the security gate record at the SITE. The CONTRACTOR’s/ SUB-CONTRACTOR’s SM/SE/SO should take care that all their vehicles shall be equipped with an audible reverse signal alarm, which operates automatically with & all times during the backward movement.
COMPANY NAME/ SUB-CONTRACTOR’s SM/SE/SO shall stipulate SITE traffic regulations:
Displayed speed limits must comply with all rimes.The speed limits for all vehicles within Project Area shall be 20 km/hour or as specified routes must be adhered to – under no circumstances may a vehicle leave the hardtop road surface. The number of passengers in a vehicle may not exceed the seating capacity of the vehicle.
- The vehicle should park side to side in car parks.
- A vehicle may not be loaded beyond its load capacity.
- Overhanging loads shall not be carried without authorization.
- The gross weight of a vehicle using a bridge must not exceed the stipulate maximum permissible load.
- Park vehicles only at designated places so that it doesn’t create hindrance to other vehicles.
- Drivers must posses’ license while driving.
- COMPANY NAME will ensure that trucks & trailers will not be used for transportation of personnel at SITE.
Note:
- A vehicle and trailer are to be considered as one vehicle
- Hazardous or corrosive materials may not be transported by vehicle within a restricted area without authorization.
- Vehicles may not be refueled within restricted areas.
- Driver to his superior must report all injuries however minor immediately.
14.FIRE PROTECTION AND PREVENTION
The best defense against fire is to prevent the fire from starting; you need to know what to do to keep on fire from starting, as well as how to deal with an accidental fire.
To ensure that fire protection and prevention are properly monitored make sure the below mentioned are present on the site.
- A portable fire extinguisher will be installed, accessible, inspected and maintained fully charged and operational.
- Proper storage of materials (Flammable).
- Good Housekeeping
- Emergency procedures should be readable and conspicuously posted on-site or in the office.
- Electrical safety must be observed.
- No Smoking Policy must be strictly implemented on-site near fabrication.
- Fire drill should be quarterly done on the site to exercise the workers on what to do in case of an emergency.
- Emergency control numbers must be posted in a conspicuous locations on site.
- HEAT STRESS
PURPOSE:
SPIG is committed to protecting the health and safety of all personnel involved in its activities as an internal part of its business management. Heat stress is a major health hazard especially in summer season, where climate is hot and humid with a temperature rising up to 45-degree centigrade and relative humidity reaching up to 70 to 80% in some parts of the country where we operate. This hot and humid climate creates a potentially dangerous situation for those exposed to the heat The company approach to protecting the health of its personnel in such areas is to provide a safe working environment by minimizing their exposure to such hot and humid conditions and its adverse health effects. In order to achieve this objective, we follow the basic occupational health and industrial hygiene principle i.e Recognition, Evaluation and Control.
Scope:
COMPANY NAME Heat prevention and management guidelines addresses heat stress identification, evaluation and control to implement to reduce various effects of heat stress-ranging from heat cramps, heat syncope, heat exhaustion and heatstroke among the workers.
Prevention Guidelines:
The primary hazard to be controlled is a heat-related illness. There are three primary illnesses associated with excess heat strain on the body that this document will address. They are heat cramps, heat exhaustion, and heatstroke. When the human body cannot maintain the internal body temperature or electrolyte balance, illness can develop from the heat cramps to heat exhaustion and finally to heatstroke. There are two major factors affecting body temperature when working in hot environments.
Establish a complete heat illness prevention program, provide training about the hazards leading to heat stress and how to prevent them, provide a lot of cool water to workers close to the work area, at least one pint of water per hour is needed.
Modify work schedules and arrange frequent rest periods with water breaks in shaded or air-conditioned areas, gradually increase workloads and allow more frequent breaks for workers new to the heat or those that have been away from work to adapt to working in the heat (acclimatization), Designate a responsible person to monitor conditions and protect workers who are at risk of heat stress, consider protective clothing that provides cooling.
- HOISTING AND LIFTING PROCEDURES
Any equipment’s use for hoisting works shall be certified by the third-party inspector prior to its full operations. Any types of lifting equipment’s must be operated by the certified and competent personnel in compliance to the instructions provided by the manual procedures. All works involving the use of crane should be planned and rigging study should be carried out to ensure that.
CLICK HERE FOR? LIFTING SAFETY
Follow the safety procedures before commencing the hoisting and lifting works.
- The capacity of the crane should be ascertained before using. Brakes should be checked while lifting critical load and adjusted if needed.
- Crane should never be overloaded.
- Check remote operations.
- Make sure the switch limit is in good condition and available.
- Check the condition of safety hook and latch.
- Carry out a functional test of the hoist switches, to ON and OFF, operate UP and DOWN then note if it’s the response.
- Check emergencies stop button.
- Verify the weight of the material intended to lift.
- Check the lifting tackle associated with hoist.
- Competency of the operator.
- Simultaneous activities around the hoist.
- Provide adequate barricade and signage to avoid other workers entering the area where lifting operations is on progress in the factory and sites as well.
- Safe working load of any mobile crane depends on:
(a) Operator’s Skill
(b) Condition of ground
(c) Boom length
(d) Radius of rotation while lifting the load, inclination of boom to the vertical
(e) Outrigger blocked/free
(f) The safe working load is generally tabulated in the load chart of the crane. Sometimes crane are de-rated due to defects in welding, bend in angle, bracings and condition of clutch, brakes etc
(g) The load is the total load hung from the rope sheaves of the boom including the weight of hook block, ropes/sling etc
17. HOUSEKEEPING PLAN
It is very important that the subcontractors and suppliers follow and maintain the approved Housekeeping plan.
Housekeeping means there is a place in everything, and everything is in its proper place. It is everybody’s business to observe it in the workplace. Housekeeping is also important it lessens accidents and related injuries and illnesses; it, therefore, improves productivity and minimizes the direct and indirect cost of accidents/illnesses.
17.1 Good Housekeeping means:
- Sweep up and remove daily all kinds of waste e.g. packing material, cotton waste, grinding wheels, FRP scrap, etc. leave clear space around storage and ensure unobstructed access to firefighting purpose and emergency evacuation. SPIG shall ensure good housekeeping at site by regular monitoring of the worksite by supervision and providing training and the importance of housekeeping. Waste container provided for at site and an office area for collecting the waste generated.
- Temporary electrical cables shall be so installed as not to cause a tripping hazard to personnel, nor be liable to Mechanical damage by the equipment.
- Return all surplus material to the stockpile at the completion of your job.
- Do not leave tools and materials where they will create a hazard for others. Put them in the gang box or return them to the tool room.
- Place oily rags in approved metal containers.
- Separate manpower shall be provided for daily housekeeping at SITE.
- Wipe up spilled liquids immediately. If you cannot handle the problem, notify your supervisor so that he can arrange for the necessary clean up.
- Keep change rooms clean. Do not let soiled cloths, food scarps, and soft drink bottles accumulate. If drinking cups are us deposit them in the containers provided. Also place sandwich wrappers, paper bags and others trash in these containers.
- Toilets, wash-up facilities, and drinking fountains are provided for your convenience and comfort. Please help keep them clean and sanitary. Report any problem to your supervisor.
- WORKING AT HEIGHT
Where work at height is required the team leader will ensure that all such work is properly controlled and that safe access and working platforms are provided in accordance with statutory requirements. The team leader will ensure that all scaffolding is erected, altered or dismantled only by competent, trained, experienced personnel under the immediate supervision of a competent supervisor.
Contents
CLICK HERE FOR? SCAFFOLDING
All scaffolds will be of sound construction and be properly maintained and inspected by competent person. Where the provision of scaffolding for work at height is impracticable other safe working methods or systems will be used. This may be in the form of a mobile elevated work platform, or the provision of fall arrest equipment provided. Where such alternative methods are used a system of work will be devised to ensure that all aspects satisfy the relevant statutory provision and provide the personnel involved with a safe place and system of work. Any work 1.8 meter & above need proper work platform & use personal fall arrestor.
CLICK HERE FOR? WORK AT HEIGHT SAFETY
Where such alternative methods are used a system of work will be devised to ensure that all aspects satisfy the relevant statutory provisions and provide the personnel involved with a safe place and system of work.
Entire height work crew shall have gone through working at height training by SPIG
- PERMIT TO WORK SYSTEM (PTW)
COMPANY NAME shall follow CLIENT permit to work system all types of work connected with Construction shall be
carried out under a work permit system.
- The most formal method of ensuring safe working practice – a safe system of work – is to have a permit to work procedure. A permit to work system shall ensure that a trained authorized person shall pre-assess the hazardous circumstances involved and then prescribe the conditions and limits for the work to take place.
- The permit certificate requires acknowledgment by the performing authority (team leader) that is responsible for doing the work to indicate that working conditions and limits are thoroughly understood.
Work permit Requirement
Work permit systems are the most formal method of ensuring safe systems of working. Their use shall be reserved for work where there is potential hazard and that the precautions necessary for that work need positive enforcement.
Issuing Authority: – is the person who signs a work permit and authorizes the work to start, provided that all the prescribed special conditions have been or shall be complied with? He shall ensure that all supporting documentation has been obtained and is properly completed before the work permit signed.
Performing Authority: – is the person who receives the Work Permit, normally a supervisor of the operatives carries out the work. He shall ensure that he, and all the operatives involved, understands the conditions, limitations, and precautions necessary as stipulated in the Work Permit, and that these are complied with
- ELECTRICAL SAFETY
Electrical supply systems shall be maintained in a safe condition and electric connection for construction power shall be provided as per CLIENT procedures all portable electrical equipment shall be 220 volts or lower. All overhead supplies shall be protected with suitable goal posts and prominently placed precautionary signs. Regular checks and inspections shall be carried out on all electrical equipment’s and recorded with the notice on the piece of equipment confirming it is safe. Proper cable management shall be maintained at the site for all times. All lighting cables shall be buried or at least 2 meter over the ground. And where road crossing is their cable shall be buried with appropriate casing pipe. Besides these following precautions shall also be taken:
- All switchboards, extension boards, etc, should be protected from rain and water. No water logging shall be allowed around switchboards.
- Earth leakage circuit breakers should be provided on all distribution boards and main switchboards.
- All fuse shall be of good quality and conform to correct ratings, use of makeshift wire or conductors.
- ELCB or RCCB will be provided. ELCB trip rating, not more than 30 mA.
- A qualified electrician will be available at site.
- Proper earthing will be available for each distribution board.
- All distribution boards and the electrical facility will be properly protected from rain, construction water.
- While working on electrical equipment and facilities, the power supply must be disconnected and LOTO system must be provided,
- Working on energized circuit/live wires is strictly prohibited.
- Electrical maintenance must be used wooden platforms, use lockout & tag out, insulated tools and rubber boots.
- While crossing the overhead electric line, all operational movements of excavators, cranes, tractors and all other tall items of equipment have to be carefully observed.
- Replace or repair defective cable immediately.
- All fittings shall be weatherproof industrial type.
- Cable shall not be fixed in plug without plug top.
Temporary electrical installations
Only authorized and competent personnel shall install all site electrical supply systems and shall be responsible for the control of all maintenance and repairs to any electrical switchboard, distribution board, hand tools. All electrical equipments should be inspected and certified as safe for use prior to commissioning. The provision of all connections and equipment required shall be in accordance with these safety conditions and comply strictly with applicable Electricity Rules.
- SANITATION ON SITE
Sanitation is extremely important on-site or plant; it helps to maintain good health and tidy environment where numerous people are working daily.Here are some sanitation facilities that are required to be available on-site or in-plant.
Water
- There should be an approved portable water system use for the distribution of drinking water.
- Ensure that drinking water is free from any contamination that can affect the health of the workers.
Toilets
- Toilet facilities must be provided on a construction site/plant prior to full operation.
- Make sure that a number of toilets can accommodate the number of people working on-site and it should be monitored and maintained every day to ensure its cleanliness.
Washing Facilities
- Washing facilities will be provided as needed to maintain healthful and sanitary conditions, particularly to those workers who engaged in the application of paints, insecticides, or any substances where contaminants are harmful. Each washing facility shall be provided by water and soap to maintain its sanitary condition.
- HAND AND POWER TOOLS
- All power tools will be inspected tested to determine its safe operating condition and proper maintenance.
- All hand tools will be in good working condition and shall use only for the purpose-designed.
- Electrical hand tools shall be replaced immediately if there is the sign of any damages.
- Use of tools shall be in accordance with the safety requirements of standard safety manual.
- Steel Engineering Technology shall strictly comply with all manufacturers’ instructions regarding specific use and maintenance of power and hand tools. MSDS (Material Safety Data Sheet) should be provided by the manufacturer to the consumer for additional details.
- Steel Engineering Technology shall not issue or permit the use of unsafe/defective power and hand tools. Such tools shall be promptly removed from service and repaired/discarded.
- All hand tools and power tools shall be kept in proper and tidy place after use.
- SCAFFOLDS SAFETY
- General
Before starting work on a scaffold, inspect it for the following:
- Are guardrails, toe boards, and planking in place and secure?
- Are locking pins at each joint in place?
- Are all wheels on moveable scaffolds locked?
CLICK HERE FOR 👉 TYPES OF SCAFFOLDING
CLICK HERE FOR 👉 SCAFFOLDING FULL DETAILS
CLICK HERE FOR 👉 SCAFFOLDING CAPACITY
- Do not attempt to gain access to a scaffold by climbing on it (unless it is specifically designed for climbing – always use a ladder.
- Scaffolds and their components must be capable of supporting four times the maximum intended load.
- Any scaffold, including accessories such as braces, brackets, trusses, screw legs, ladders, etc., damaged or weakened in any way, must be immediately repaired or replaced.
- Scaffold planks must extend over their end supports not less than 6 inches nor more than 12 inches, unless otherwise specifically required.
- Scaffold platforms must be at least 18 inches wide unless otherwise specifically required or exempted.
- Where persons are required to work or pass under the scaffold, scaffolds shall be provided with a screen between the toe board and guardrail, extending along the entire opening. The screen must be made of No. 18 gauge U.S. Standard wire, ½ inch mesh or equivalent protection.
- All scaffolds must be erected level and plumb, and on a solid footing.
- Do not changes or remove scaffold members unless authorized?
- Do not allow workers to ride on a rolling scaffold when it is being moved. Remove or secure all materials and tools on deck before moving.
- Do not alter any scaffold member by welding, burning, and cutting, drilling, or bending.
- FIRST AID PLAN AND FACILITIES
The medical team and first aid supplies must available on site to ensure instant rescue will be done appropriately during the event of an emergency such as fatal accidents, fire or illnesses occurred on-site/plant.
- First Aider/Company Nurse should be available on-site or plant all the time whenever the work is on progress.
- First Aid stations must be accessible on-site/plant to all medical facilities and easy to locate to avoid inconvenience during the event of an emergency.
- All possible emergency services such as telephone numbers and addresses such as hospitals, doctors, poison control centers, fire departments, ambulance, etc. are known listed and provided by the client.
- First aid supplies should be monitored to avoid the deficiency of each item.
- The first-aid arrangements should cover shift working, night and weekend working where this is work carried out. This may mean appointing or training several people to ensure adequate cover.
- Report all inquiries immediately, no matter how minor, to your supervisor and to First Aid. Treatment will be given, and the Incident will be recorded. Should later medical care be needed, you will have fulfilled your obligation.
- You must notify your supervisor and First Aid prior to leaving the job site because of injury or illness, whether personal or work-related.
- If you get outside medical treatment (without clearing through First Aid) for a work-related injury of illness, you must notify First Aid at the start of the next scheduled workday. Failure to do so may result in disallowance of your claim and/or discharge.
- Prior to returning to work after a disabling injury or illness, you must present a medical clearance for the attending physician to First Aid.
- Drugs, tranquilizers, and insulin must not be taken on the job unless authorized in writing by your personal physician. A copy of this authorization should be in your first aid file.
- If you have a physical handicap, such as diabetes, impaired eyesight or hearing, back or heart trouble, hernia, or aversion to heights, tell your supervisors. You will not be expected to do a job that might result in injury to yourself or others.
- First aid teams are organized and trained to render assistance. In the event of an injury or illness you will get proper first aid treatment. Your physician will be notified in the event if an emergency.
- Never move an injured or seriously ill person unless necessary to prevent further injury. Emergency steps for notifying First Aid are posted through the Jobsite; familiarize you with them. First aid should not be administered by non-designated employees expect in case of severe bleeding or cessation of breathing.
MATERIAL HANDLING AND PROPER STORAGE
All material must be properly stacked and secured to prevent sliding, falling or collapse. Aisles, stairs, and passageways must be kept clear to provide for the safe movement of employees and equipment and to provide access in emergencies.
- Use proper lifting techniques when handling materials.
- Get down close to the load.
- Keep your back straight.
- Lift gradually, using your legs. Do not jerk or twist.
- Get help for bulky or heavy loads.
- The storage of material must not block any exit from a building.
- Pipe, conduit, and bar stock should be stored in racks or stacked and blocked to prevent movements.
- The quantity of material stored on scaffolds, platforms, or walkways must not exceed that required for 1 day’s operation.
- Material must never be thrown or dropped from a distance of more than 20 feet. The drop area must be barricaded to protect personnel from being struck by falling materials. Trash chutes are required for dropping materials from heights above 20 feet.
- Protruding nails must be bent or pulled when stripping forms are not in proper place/crate.
CLICK HERE FOR 👉 MATERIAL HANDLING SAFETY
26. REPORTING OF INCIDENT / ACCIDENT / NEAR MISS AND PROCEDURES
- Serious Accident
If an employee is involved in a serious accident or a major loss to equipment or property occurs, the Safety Engineer/Officer and/or the Project-In-Charge shall notify designated personnel and affected organizations so that an investigation can be initiated. The following shall be the procedure:
A1. Near miss incident / accident reporting in CLIENT format.
- Reporting Serious Accident
Upon learning of a serious or fatal accident in the project, the following personnel must be immediately notified:
- Safety Supervisor or Safety Manager or Central Safety Department
- Report to CLIENT in their format within 24 hours.
- Project Manager or his designated Project-In-Charge
- HRD Department
- Appropriate Law Enforcement Agency
- Investigating Serious Accidents
An investigation should be conducted as soon as possible after the accident. The investigation must be fact-finding, not fault-finding. Members of the investigating team should include the Project-In-charge or his representative; site Safety Engineer, the responsible Area Safety Supervisor, HR Department representative and the employee’s supervisor. The purpose of the
Investigation is to determine the real causes that similar accidents can be prevented, and also to determine facts bearing on legal liability. A description of the operation being performed at the time of the accident is essential. All personnel assigned to the operation and all witnesses to the accident shall be interviewed and statements taken. A private place such as an enclosed office or conference room should be used for these discussions.
The interviewers (2) must obtain hand facts and not hearsay. The information obtained must be recorded and signed by each person involved.
- Date and time of the accident.
- Name, badge or I.D., numbers, address, and occupation of victim, co-workers and/or witnesses.
- Location of the witness when the accident took place.
- What activity is being performed prior to and at the time of the accident?
- What materials, equipment or conditions were involved? Include all contributing factors.
- What happened?
- Why did it happen? Include all unsafe condition and/or unsafe acts.
- To the best of witness knowledge. Was there a previously known/or reported problem or condition associated with the accident?
- Photographs and Drawings
Drawings and/or sketches indicating the location of the accident must be made. All measurements such as time, distance, etc. must be accurate. Photographs should be taken as soon as possible since conditions often change rapidly. The back of each photograph should contain the following information: description and location of the principal item (S) date and time, name of the photographer.
- Evidence
Immediately after the accident, the area must be secured in order to prevent any alteration of the scene prior to the investigation. If equipment, tools and materials are involved in the accident, they shall be removed temporarily from the service and placed in safekeeping. If this is
impractical, the area shall be cordoned off and a security guard posted to prevent unauthorized personnel from entering the area.
- Recordkeeping Procedures
The project nurse provided by Main Contractor or First Aid Station personnel must maintain a variety of records. For the protection of the employees, medical personnel, the company and client.
- First Aid Log
This is a chronological listing of all visits to the First Aid Station. Every injury or illness reported, no matter how slight must be recorded. A copy of the logbook and necessary forms shall be provided to the First Aid Station.
CLICK HERE FOR 👉 FIRST-AID
And also report to CLIENT within 72 hours in their format.
- Individual Medical Record
This is confidential record of the employee’s illness and injuries reported to the clinic or First Aid Station. The project nurse of First Aider is responsible for keeping the medical record of every employee in the site. At the end of the month, he/she shall submit to the Project-In-Charge and Safety Engineer a summary report of all cases treated in the clinic.
- Injury Reporting and Recordkeeping Procedures
Duty of First Aider shall promptly accomplish the Clinic Accident Report which must be distributed to the following office:
- 1 copy – Safety Department CLIENT
- 1 copy – Personnel/Records
- 1 copy – Department where injured is assigned
- 1 copy – Clinic File for authority’s formalities if serious injuries
The nurse should obtain the necessary information to complete the report.
- Supervisor’s Accident Investigation Report
The Supervisor’s Report of Accident Investigation shall be prepared and submitted within 24 hours after the accident. The Foreman/Supervisor shall investigate the accident and fill up completely the form and furnish copy to the abovementioned offices. A standard report format is provided to assist as a guide to the investigator.
- Corrective Action
The Supervisor/Foreman shall specify what corrective action if any, was taken Instruction given, etc. If corrective action is not applicable, indicate same on the report.
IN THE EVENT OF FIRE:
- Immediately shut off the source of power supply.
- Immediately inform to CLIENT fire department.
- Raise the alarm to aware everyone inside the building and offices.
- Use fire fighting equipment’s such as fire extinguishers, fire hose reel, etc. if you are trained to do so but don’t put yourself in danger.
- Immediately leave the building or office and seek the emergency exits and proceed immediately to the assembly point.
- Never attempt to use elevators during the event of fire; it will lead you to danger.
- Relax and don’t panic because it will lead you to injury or even death.
- In case you are suffocated, simply drop the ground and inhale since there is existing oxygen over there.
- When you reach the assembly point, stay calm and inform your supervisor if there is still missing in your group. The supervisor should do the headcount to his people as soon as possible.
- Do not attempt to re-enter the building unless there is a further notification coming from Area Controller (Project Manager, HSE Personnel).
- Inform to CLIENT in their format within 24 hours.
IN THE EVENT OF INJURIES:
- Immediately inform the area supervisor, HSE personnel, and Senior Management for immediate assistance of the injured worker.
- Do not attempt to administer first aid to the injured worker if you are not trained to do, let the first aider to administer first aid.
- Call enforcing authorities such as Senior Management, HR, Projects Manager and HSE Experts, and Investigative team for an immediate investigation to determine the immediate causes of accidents and to prevent the recurrence.
- Inform the relatives and friends of the injured worker.
- Inform to CLIENT in their format within 72 Hours.
Safety plan for construction site
If you not able to download this document please email at rlsumancare@gmail.com
Also, read this:
QHSE PLAN
HSE PLAN
EHS PLAN
SHE PLAN
You are reading at rlshumancare.com. Do not forget the name RLS HUMAN CARE. Please share with your friends and help RLS HUMAN CARE. Thank You!!
PLEASE SHARE THIS ARTICLE WITH YOUR RELEVANT FRIENDS
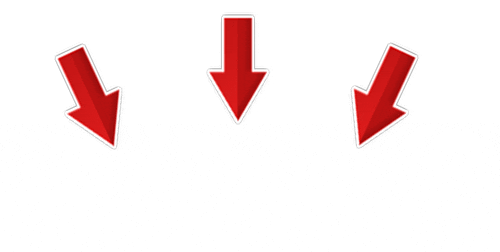
this plan we can apply for oil&gas refinery
Yes!!
good share
Thank you sir for sharing your knowledge…..?
i like this page
how to make HACCP PLan for food industry
https://www.uoguelph.ca/foodscience/book-page/haccp
good stuff
Very usefullcan implement at place of work