Care in design, operation, and maintenance of any lifting equipment is utmost necessary. It includes many points some of which are common and some specific points differ with the type of machine.
Some Common Points of Care:
Design | Operation | Maintenance |
The appropriate factor of safety. Sound material & Good construction. Safe design. Marking of SWL & identification. Provision of limit switches, brakes, anchoring, earthing, guarding, means of access, ladders, etc. | Trained operator No loading above SWL. Moving hook load safely. Use signaling & warning. Raise or lower carefully. Following the manufacturer’s instruction. Work on or near tracks. No-load handing over workers on the floor. Safe position at the end of work. | Periodical tests and certification. Lubrication of parts. Repairs and replacement of parts. Daily and periodical inspection. Display of notices and load tables. |
Some specific points are mentioned below:
Hoist & Lifts: Dos and Don’ts of safe operation should be followed. Safety devices and interlocking should be well maintained. Regular testing and examination are necessary.
Lifting tackle or gear: If more than 10% wires are found broken or wear on any stress-bearing part exceeds 10% of the requisite nominal dimension or the part shows signs of excessive wear, corrosion or other defects, it should be considered unfit for service.
A testing period of lifting machinery and tackles, prescribed by the Factories Act is one year. A test certificate specifying the SWL is also necessary (Rule 60, Form 10, GFR).
Metallurgical Defects and Heat Treatments: Ferrous and non-ferrous metals are used to make lifting gear. Monel metal (2/3 nickel, 1/3 copper, a small percentage of manganese and iron) is highly resistant to corrosion. Chain and other lifting gear made of Monel metal are suitable for use in chemical plants.
Copper is the main constituent in brasses and bronzes. They are mainly used for bearing in lifting gear.
Aluminum and manganese bronze has high strength, ductility, and corrosion resistance. They are used to make chains and fittings where higher corrosion resistance is required.
During the welding process, the adjacent material is subjected to intense local heat and becomes brittle on cooling, Links, rings, and chains required heat treatment to correct this coarse structure.
In the process of forging, drop forging steel is highly heated to have the desired shape. Then the structure becomes brittle. With hammering or hot work the grains size in the material changes.
Defects are also developed during service. Due to interlink pounding, wrought iron develops surface brittleness. Due to the bending strain, the link becomes hardened and develops a crack. Over a period it results in link fracture.
Internal hardness can develop both in wrought iron and steel gear due to overloading. Improper use causes a reduction in ductility. Certain low carbon steels are liable to strain-aging.
Rings, hooks, links, etc. used in a sling must be of the same material and of equal strength as the chain.
Heat treatment (a series of operations involving heating and cooling of metal parts) – Low-temperature annealing, normalizing, hardening, and tempering should be carried out as per requirement.
Heat treatment like normalizing or hardening and tempering can restore the strained parts to the original condition provided no crack has taken place. Type of heat treatment is – low-temperature annealing, normalizing, hardening, and tempering. thus such metallurgical defects should be detected by proper insection and necessary heat treatment be applied.
Defect and Precautions: Stretch or deformation, excessive wear, cracks, nicks, gouges, and corrosion pits – should be searched by proper inspection procedure and removed.
The selection of proper rope and inspection before use is important. Workers should be thoroughly instructed to follow the safe operating procedures in using ropes and chain slings. They should be kept away from heat, fumes, chemicals and exhaust gases. They should not be used against sharp edges. Protect them by padding. Observe proper slinging rules. Do not exceed safe slinging angles. Check for friction heating for fiber ropes.
No tackle should be dropped from heights. They should be stored in clean dry place.
Contents
Inspection of tackles:
Lifting Tools and Tackles | Period |
Hoisting and lowering wire rope | 3 months |
Wire ropes with the broken wire | 1 month |
Cranes and attachments | 12 months |
A thorough inspection of all parts of the crane | 3 years |
All other liftings machinery | 12 months |
Half inch and smaller gear | 6 months |
All items used in lifting machinery should be subjected to proof test loads and after the test, they should be thoroughly examined by a competent person for signs of cracks, fatigue, deformation, stretch, etc.
Hooks must be removed from service if they have opened out more than 15% of the normal throat opening, measured at the narrowest point or twisted more than 10 degrees from the original plane of the hook. The bent hook should not be straightened and reused.
A locking pawl prevents the load to come out from the hook.
Fiber ropes should be inspected before use every time. Broken fibers, yarns, cuts, nicks, abrasion, unlaying and reduction in diametre are the main defects. If the fibers pulled from the rope breaks, it shows brittleness and needs to replace the rope.
Wire rope should be inspected for broken wires, torn, flattened and abraded wires, reduction in rope diameter, rope stretch, corrosion, kinks, crushed or jammed strands, bird caging and inadequate splices.
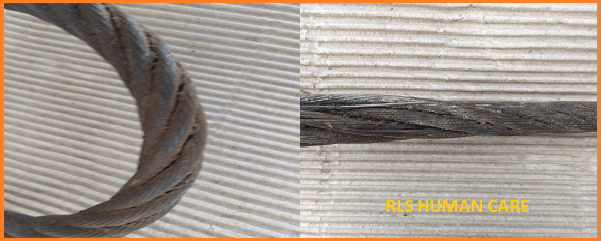
New lubricants, free of grit should be applied on wire rope to penetrate internally as well as to coat the external surface.
Defect in wire ropes is broken wires, abraded wires, reduction in rope diameter, rope stretch, corrosion, kinks, crushed, flattened or jammed strands, bird caging and damaged splices. In such cases, a new wire rope should be used.
The visible broken wires should not be more than 5 % of the total wires in length of 10 rope diameter. Wear on the surface of the rope should not be more than 1/3 of the diameter of the wire. In pendants or stranding ropes, there should not be more than 3 broken wires in one rope lay.
Rope stretch should not be more than 15 cm per 30 m length in the six-strand wire ropes. Ropes should be discarded if more than 20 breaks appear on a rope lay.
Reduction in diameter of the rope due to core failure, abrasion, etc. should not be more than-
1.0 mm for ropes up to 19 mm dia
1.5 mm for ropes of 22 to 28 mm dia
2.0 mm for ropes of 32 to 38 mm dia
Chains: Most of the causes of chain failures can be detected before they occur if proper procedure is followed. The frequency of such inspections depends on service conditions. Normal defects are (1) stretch or deformation (2) excessive wear (3) cracks (4) nicks and gouges and (5) corrosion pits.
Chains are to be checked for crack, corrosion, and pitting. More than 10% wear at their two-link-touching point render them unfit for use. Avoid jerks and impact loads. Never re-weld alloy chain links. Avoid crossing, twisting, kinking or knotting chain.
The causes of chain failure are defective weld, defective metal, and overloading. all chains should thoroughly be inspected link by link by a competent person. Aftershock or impact loads, it must be immediately inspected. It is an unsafe method to use the broken chain by inserting a bolt between two links.
Clean the chain thoroughly in a solvent solution. Lay it on a clean surface. Use the magnifying glass to look for stretched links, wear, crack, corrosion and pitting, bent, twisted or damaged links. If stretch (elongation) is more than 3 % the chain should be discarded. Elongation should be measured between a fixed length of 10 or 20 links.
When the dia of the link is reduced due to wear and tear, SWL shall be reduced as under:

Shackles worn more than 10% of the original diameter in crown or pin should be replaced. Pins should not be bent. Shackles shall not be pulled at an angle because it will reduce its capacity.
You are reading at rlshumancare.com. Do not forget the name RLS HUMAN CARE. Please share with your friends and help RLS HUMAN CARE. Thank You!!
Chain pully blocks of proper lifting capacity should only be used. they should be lubricated before every use. No alternation should be done on chain-blocks. They should be tested for a slip by suspending a safe load. The chain should not come out of pulleys. The anchoring should be strong and rigid. Opened out hooks should not be used. Chain blocks/pulleys must be checked if stored for a long time, by subject to shock load, to observe slipping of load, jamming on links, etc.
Winches should be placed on a firm base and properly anchored. Brake, ratchet arrangement, gear and pinion including meshing, wire rope and clamping arrangement, the direction of receiving rope drum and tie rods should be checked before using any winch.
Derrick – The mast, guy-ropes, wire ropes, swivel hook, rope clamps, etc. should be thoroughly checked before erecting the derrick. Its lifting capacity should be ascertained by a competent person and it should not be overloaded. Guys of the derrick should be anchored tightly with strong structures, holdfasts, anchorage blocks, etc. Welded parts should be periodically checked for any crack or defects in the metal itself.
Mobile Crane should not be used on a slope unless adequate precautions are taken to ensure stability.

SWL of cranes applies only when they are installed on a level, firm and uniform surface. Crane stability is reduced when operating on a slope. Therefore level must first be checked. It is dangerous to lift a load with 2 cranes and should be avoided unless a single crane of the required capacity is unavoidable. Trapping or striking with persons should be avoided.
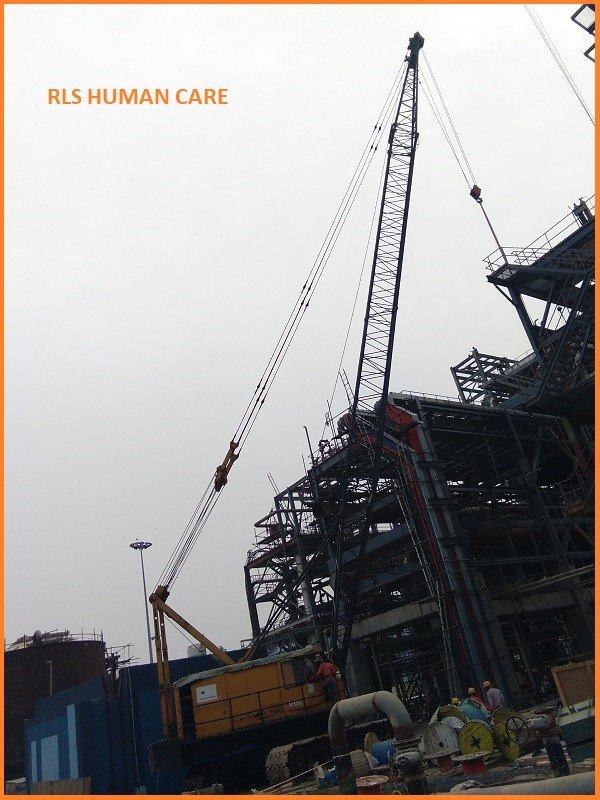
Jib or boom of a mobile crane should not touch any electric wire or loose construction which may fall. When any overhead material handling works is going on, simultaneous work down below must be avoided to eliminate the risk of being hurt by any falling material.
Mobile crane should be parked on hard soil or a strong base. The tag line should be used during lifting any materials. The brakes, boom, hook, wire ropes, pulleys, and rope anchoring should be checked periodically by a maintenance man to ensure the safe operation. Required derating should be done in case of any defects found and it should be formally made known to all concerned.
In case of mobile crane, the load shall be derrick out while going up a gradient and the load shall be derrick into the minimum radius while going down.
Mobile cranes are to be tested for (1) A dynamic test of 10% overload (2) Test with 25% overload and (3) Static stability test.
All control mechanisms, safety devices, hydraulic systems, hooks, running ropes and electrical apparatus of a crane should be inspected frequently for malfunction, wear, deformation crack, fluid leak, dirt and moist accumulation, etc.
Defect to be checked in a crane are:
- Deformed, cracked or corroded members of crane, structure, and jib.
- Loose bolts or rivets.
- Cracked or worn sheaves and drums.
- Worn or damaged pins, bearings, shafts, gears, rollers, etc.
- Excessive wear on brakes or clutch parts, linings, panels, and ratchets.
- Diesel, electric or other power units for improper performance.
- Excessive wear on a chain drive, sprocket and excessive chain stretch.
- Travel, steering braking and locking devices for malfunction and
- Excessively worn or damaged tires.
During repair and maintenance, permit to work system should be followed. A preventive maintenance program, based on the crane manufacturer’s recommendations should be established.
All moving parts should be regularly lubricated and lubricant levels should be checked.
Crane operators should be of more than 18 years of age and properly trained, medically fit with regard to eyesight, hearing, and reflexes, and understand fully the duties of the slingers and be familiar with the signal code.
Documentations for record of inspection and maintenance and test certificates are equally important.
Safe Location
A safe location or storage of lifting tackles is necessary.
Proper storage of chains will impress the workers they need for proper care at all times. The chains should be hung on racks in dry air and normal temperature to prevent rusting. Racks should be so arranged that no worker should be exposed to lifting hazards. Heavy chains may be stored in neat piles on a rack surface. Dampness, darkness and corrosive atmosphere should be avoided.
The sling should be kept on suitable racks when not in use. SWL should not be exceeded as a result of the angle between the legs.
Store the ropes in a dry room having good air circulation. Hung the ropes up in loose coiled in pegs. Clean the rope after use and dry them before storing it. Fiber ropes should be protected from pests, rats, sun, weather, and dampness.
Also, read this:
Safety in rigging and erection operation
Construction site safety checklist
24 points for crane inspection
You are reading at rlshumancare.com. Do not forget the name RLS HUMAN CARE. Please share with your friends and help RLS HUMAN CARE. Thank You!!
sir pls tell me how to check the rpm of a grinder machine and cut-of-saw machine
If I own a construction business, I would understand how important it is that machines are repaired and maintained quickly with the proper undercarriage parts replacements. Now I know that a safe working load could be achieved in cranes only when they operate on a leveled surface. Also, lifting using two cranes should be avoided and only be done in certain situations. I hope that if I get into this line of business. there will be repair services that could help me maintain the top machine working standards.
very good HSE platform for enhance your knowledge and confident.
I want to say that please droped construction safety related posts high rise building.
Very good sir
Thank You, sir,