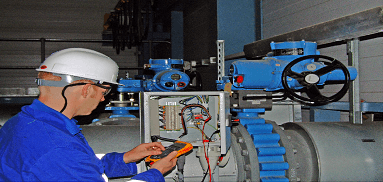
Instrument System for safety
Use of instrumentation for safety is equally important. Process parameters are well known because of the fixed objectives and therefore instrument system for process control developed first. Instrument system for safety developed at a later stage based on learning from accidents and thinking of remedial measures.
Types of instrument system for safety include fail-safe design, trip, alarm, interlocks, gas, smoke and fire detectors, toxic detectors, reaction runaway detectors, logic systems like PLC, DCS etc.
Some basic principles for safety instrumentation are as under:
- Instead of providing elaborate or complex instrument system, the hazard should be reduced at source.
- HAZOP study should be conducted to assess potential hazards, operating difficulties and instrumentation necessary.
- The measurement should be of direct variable and auto direct location.
- While designing alarms, other factors like instrument failure, operator confidence, his information load etc. should also be considered.
- As far as possible instrument design should be fail-safe.
- Range of the instrument should be sufficient so that even low input can be measured.
- Control system should be capable of dealing with normal and abnormal conditions e.g. start-up and shut down.
- In case of failure of auto controls, manual controls should also be provided for safety.
- Fault finding instrument should not be disturbed by the fault itself.
- Service instruments (e.g. for air, power, inert gas) should have give integrity.
- Instrument should be checked regularly and repaired quickly.
- Instrument design should be such that it should indicate it is fault easily. The process operator should be trend to find such fault as a part of his duty.
- Test should correspond as nearly as possible to the expected plant conditions. It may pass a workshop test, but may not perform satisfactory on the plant.
- Valves may stick or jam, jamming in the open position is dangerous. More positive isolation may require double block and bleed valves.
- Human error should be fully considered. Ergonomic principles should be applied to reduce human errors as far as possible.