Contents
Introduction to Maintenance Strategies
Maintenance strategies play a major role in the operational efficiency of various industries, ensuring that equipment functions optimally and consistently. Among the most widely recognized approaches to equipment maintenance are preventive and reactive maintenance, each serving distinct purposes in the overall maintenance framework. Understanding these strategies is most important for organizations aiming to enhance productivity and operational reliability.
Preventive maintenance refers to the systematic upkeep of equipment through regular inspections and scheduled servicing. The primary goal of this approach is to prevent equipment failures before they occur, thereby extending the lifespan of machinery and minimizing unexpected downtime. By employing preventive measures such as routine checks, lubrication, and component replacements, organizations can maintain high levels of operational efficiency and reducing the risk of costly repairs or interruptions.
On the other hand, reactive maintenance, also known as corrective maintenance, is employed in response to equipment failures. This strategy focuses on addressing issues as they arise, which can often lead to unplanned downtime. While reactive maintenance can be urgent repairs, it has drawbacks, including increased costs and potential disruptions in workflow. Industries that heavily rely on machinery benefits from a balanced approach that incorporates both types of maintenance.
The relevance of these maintenance strategies cannot be overstated. Industries ranging from construction to manufacturing and transportation rely on equipment functioning at peak performance. By understanding the nuances of preventive versus reactive maintenance, organizations can make informed decisions that optimize resource allocation and enhance overall productivity. As we delve deeper into each maintenance type, the clear distinctions, benefits, and best practices will become increasingly apparent.
Preventive Maintenance: Proactive Approach to Equipment Care
Preventive maintenance is a strategic approach aimed at regularly scheduled inspections and servicing of equipment to prevent unexpected failures and costly outages. Its core principles revolve around routine checks, predictable servicing schedules, and proactive planning, all intended to sustain optimal equipment performance. By implementing preventive maintenance, organizations can enhance the reliability and longevity of their machinery, thereby ensuring a smoother operational flow.
Implementing an effective preventive maintenance program often entails various best practices. Firstly, organizations should develop a detailed maintenance schedule based on the manufacturer’s recommendations and usage patterns. This ensures that critical equipment receives attention at the right intervals. Additionally, utilizing software solutions can greatly enhance the efficiency of preventive maintenance efforts. These tools aid in tracking maintenance activities, scheduling tasks, and documenting performance metrics, providing valuable insights for continuous improvement.
Preventive maintenance stands as a crucial element in the management of equipment health. By adopting a proactive maintenance strategy and leveraging modern tools and technologies, organizations can maximize equipment reliability, minimize downtime, and drive significant cost efficiencies.
Reactive Maintenance: Addressing Equipment Failures
Reactive maintenance, often referred to as corrective maintenance, is a strategy employed to address equipment failures after they occur. It is characterized by a response to breakdowns, which may involve immediate repairs to restore functionality. This maintenance practice is typically seen in scenarios where equipment failures are either infrequent or considered acceptable from an operational standpoint. Organizations often resort to reactive maintenance when the costs of preventive measures exceed the expenses related to unplanned downtime.
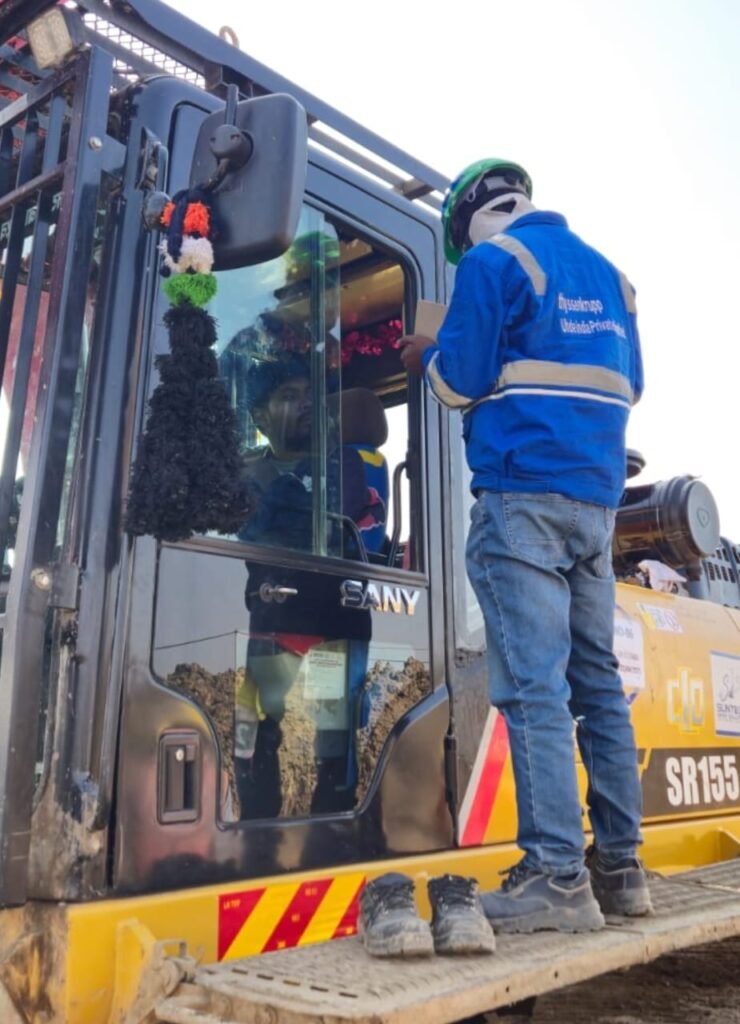
One primary consideration in reactive maintenance is timing; organizations that adopt this approach must be prepared for the implications of waiting for equipment to fail. Potential impacts on productivity can be significant, as unexpected equipment downtime can lead to halted operations and reduced output. Additionally, safety risks can arise when critical machinery fails without warning, endangering workers and potentially resulting in accidents. The costs associated with repairs can escalate as well, with emergency repairs generally being more expensive than routine preventive maintenance.
Although reactive maintenance has its drawbacks, there are scenarios where it may be appropriate. In low-risk environments, where equipment failures do not pose severe consequences, companies may find that reactive maintenance provides a viable option. For example, non-critical systems that do not directly affect core business operations can often operate effectively under a reactive maintenance model. In these cases, maintenance schedules are less rigid, allowing businesses to allocate resources more efficiently.
Nevertheless, it is crucial to balance reactive maintenance with preventive strategies. By doing so, organizations can turn downtime into opportunities for enhancement while mitigating risks associated with unexpected equipment failures. A comprehensive maintenance strategy will incorporate both preventative and reactive measures, ensuring that organizations can maintain operational efficiency while effectively managing resources.
Comparative Analysis: Preventive vs. Reactive Maintenance
The distinction between preventive and reactive maintenance fundamentally influences equipment performance, operational efficiency, and cost structure for organizations. Preventive maintenance entails systematically scheduled inspections, servicing, and repairs designed to mitigate the risk of equipment failures. By prioritizing planned interventions, organizations can avoid unexpected downtimes, ultimately leading to enhanced equipment longevity. Conversely, reactive maintenance occurs post-failure, requiring immediate attention to restore functionality. While this approach may initially seem cost-effective, the long-term implications can substantially escalate repair costs due to the often hasty, reactive nature of repairs.
When discussing cost implications, several studies highlight the financial benefits of preventive maintenance. For instance, a facility that invested in a preventive maintenance program was able to reduce breakdown-related costs by over 30%. In contrast, organizations relying predominantly on reactive strategies, although they may save on upfront maintenance costs, ultimately encounter higher expenses due to increased labor and parts costs associated with untimely repairs. Furthermore, the opportunity costs from lost production during unscheduled downtimes can significantly impact overall profitability.
Efficiency metrics also reveal that preventive maintenance fosters a culture of reliability within equipment management. According to recent reports, assets maintained through preventive techniques demonstrate more consistent performance, resulting in more predictable operational output. In stark contrast, equipment lapsing into a reactive maintenance state frequently operates unpredictably, thereby affecting the entire production chain.
To maximize outcomes, an integrated maintenance strategy that leverages both preventive and reactive methodologies can prove beneficial. Organizations should assess their unique operational demands to design a comprehensive maintenance plan. This plan may involve preventive checks to stave off failures while maintaining reactive capabilities to address unforeseen issues swiftly. Through a balanced approach, companies can optimize equipment performance while minimizing costs and maximizing productivity.